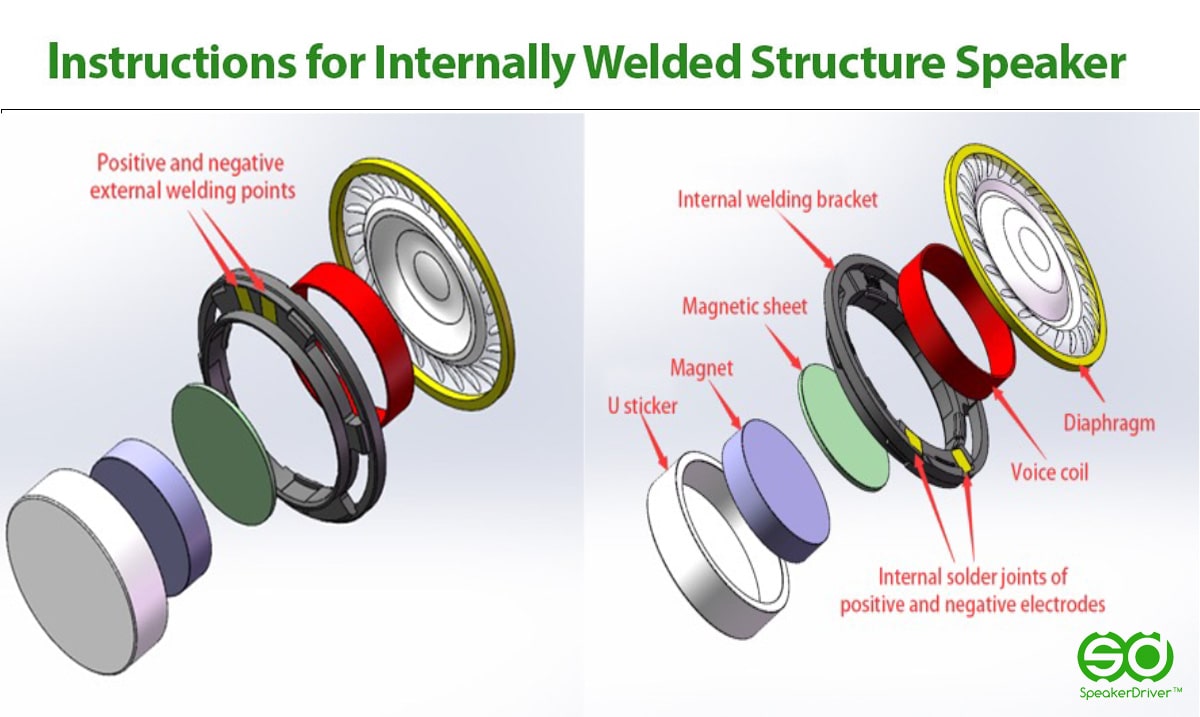
Instructions for Internally Welded Structure Speakers
Internally welded structure speakers are designed for enhanced durability, minimal resonance, and compact form factors, making them ideal for TWS earbuds, wearables, and mobile audio devices. This type of speaker unit replaces adhesives with ultrasonic or thermal welding, creating a more stable acoustic structure and improving long-term reliability in harsh environments.
Benefits of Internally Welded Structure in Speakers
- Enhanced Structural Integrity: Welding forms a permanent bond between housing parts, reducing the risk of component separation due to vibration or temperature changes.
- Improved Acoustic Sealing: The welded enclosure reduces internal air leakage, improving low-frequency performance and overall clarity.
- Consistent Production Quality: Automated welding ensures tight tolerances and reduces human error during assembly.
- Environment Resistance: Welded speakers are better protected against moisture, dust, and debris — crucial for outdoor and fitness applications.
Additional Advantages Over Traditional Speakers
- Improved Sound Quality Stability: Leads are welded inside the unit, avoiding the issues of insufficient external coverage and improving overall audio consistency and appearance.
- Optimized Production Process: The internal welding design simplifies manufacturing steps, boosts product consistency, and improves efficiency and control.
- Reduced Material Usage: With internal leads, these drivers use nearly 50% less mass than traditional externally welded models, reducing cost and weight without sacrificing performance.
- Improved Product Quality: Built-in welding parts reduce the risk of short circuits caused by external welds, increasing the reliability of the speaker unit.
- Improved Appearance Design: No exposed soldering points lead to a cleaner, more aesthetic look — essential for consumer electronics focused on sleek design.
- Enhanced Waterproof Performance: Internal welding improves sealing and limits exposure of sensitive components, boosting water resistance.
- Improved Sound Clarity: Internal design reduces external vibration and interference, enhancing clarity and sonic precision.
- Easy Integration and Design: The compact welded structure makes it easier to integrate with mobile phones, earbuds, and similar devices during final assembly.
Instructions for OEMs: Integration of Internally Welded Speakers
- Design PCB and housing layouts that accommodate non-serviceable, sealed units.
- Avoid post-assembly opening; these units are not intended to be disassembled.
- Ensure the speaker is properly positioned before welding to maintain diaphragm alignment.
- Use ultrasonic welding machines with precise frequency control to avoid structural damage.
- Conduct air-tightness tests to verify seal integrity post-welding.
Comparison Table: Welded vs. Glued Speaker Structures
Feature | Glued Structure | Welded Structure |
---|---|---|
Sealing Strength | Moderate (dependent on adhesive) | High (permanent mechanical bond) |
Thermal Resistance | Low to Medium | High |
Production Consistency | Variable due to glue application | High with automated welding |
Environmental Resistance | Limited | Excellent |
Repairability | Possible | Not Serviceable |
Common Applications
Internally welded speakers are commonly used in:
- TWS earbuds and compact Bluetooth headsets
- Wearable devices (e.g., smartwatches, fitness trackers)
- Water-resistant or ruggedized audio equipment
- Miniature speaker modules in medical and IoT devices
Conclusion
Internally welded structure speakers are a robust and reliable solution for modern audio devices requiring precision assembly and environmental resistance. Their superior advantages — including improved sound clarity, better waterproofing, reduced material use, and easier integration — make them an optimal choice for OEMs aiming to balance performance, aesthetics, and reliability in miniature speaker designs.