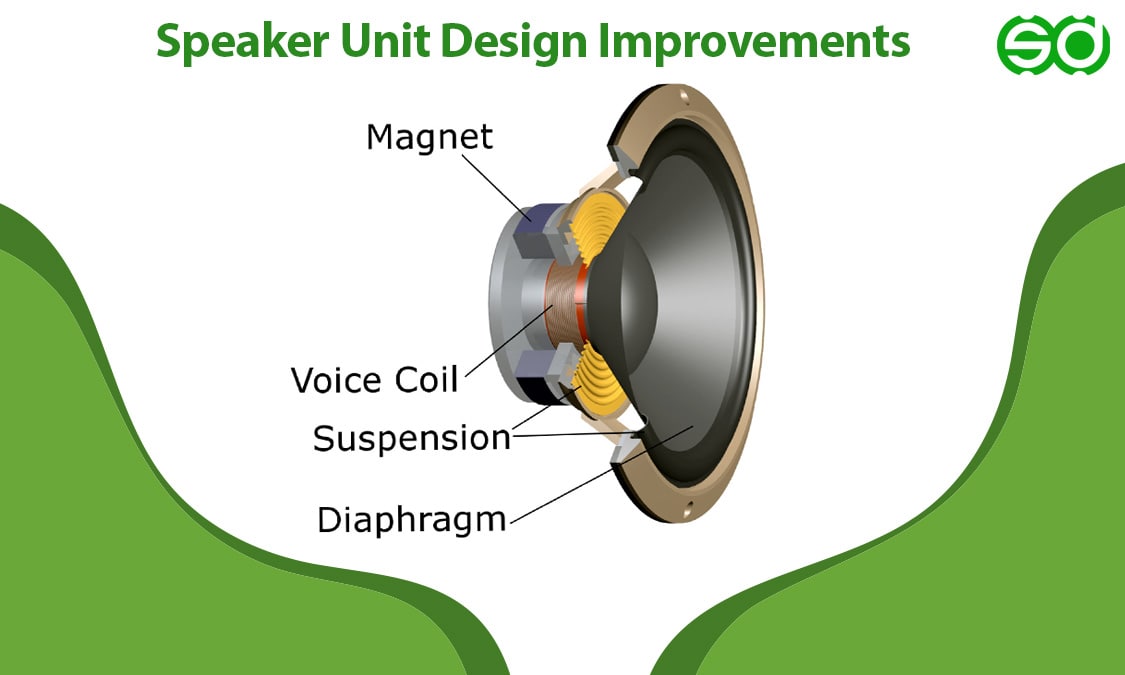
Speaker Unit Design Improvements – Advancing Micro Acoustics
Speaker unit design has seen significant evolution over the past decade, driven by the demand for more compact, power-efficient, and high-fidelity audio solutions. OEM manufacturers and acoustic engineers are optimizing everything from diaphragm materials to magnetic circuit layouts, with the goal of delivering richer, clearer, and more dynamic sound from ever-smaller driver units.
Key Focus Areas in Modern Speaker Unit Design
- Diaphragm Materials: Improvements in diaphragm composition (e.g., PET, PEI, graphene, and composite blends) allow better stiffness-to-weight ratios, reducing distortion and improving response time.
- Voice Coil Efficiency: Use of copper-clad aluminum wire (CCAW) and ultra-thin windings enhances energy efficiency and reduces thermal losses.
- Magnetic Circuit Refinement: Neodymium magnets and optimized yoke structures improve magnetic flux, boosting sensitivity while conserving space.
- Suspension Design: Better damping systems and thinner suspensions improve diaphragm control, enhancing low-frequency response and stability at high volumes.
- Acoustic Damping and Venting: Tuning rear cavity volume and airflow minimizes unwanted resonances and improves bass performance in micro enclosures.
Key Speaker Design Improvements
1. Optimize the Diaphragm Material
Choosing a lightweight and rigid diaphragm material, such as paper, plastic, or metal, can improve the transient response and frequency response of the mylar speaker.
- Choose the Right Material: Diaphragm material should be rigid, lightweight, and have appropriate damping properties. Common materials include paper, plastics (e.g., polypropylene, polyester), metals (e.g., aluminum, titanium), and composites.
- Optimize Diaphragm Shape: The shape and size of the diaphragm affect its vibration characteristics. Through simulations and testing, the optimal diaphragm shape can be determined to minimize distortion and achieve ideal frequency response.
- Improve Diaphragm Support Structure: Optimizing support structures like suspension edges and folding rings enhances diaphragm movement and reduces nonlinear distortion.
- Use Damping Materials: Damping materials reduce unwanted vibrations, reducing distortion and improving clarity.
- Multi-layer Diaphragm Design: A multi-layer diaphragm combines different material advantages, with lighter outer layers for high frequencies and rigid inner layers for low frequencies.
- Surface Treatment: Coating or plating the diaphragm surface reduces friction and increases rigidity.
- Precision Manufacturing: High-precision manufacturing ensures consistency and quality.
- Heat Treatment: Heat treatment can improve mechanical properties, such as diaphragm stiffness or reducing mass.
- Environmental Adaptability: Materials should maintain acoustic properties in varying environmental conditions, such as temperature and humidity.
- Cost-Benefit Analysis: Ensure material performance meets cost requirements.
2. Improve Magnetic Circuit Design
- Optimize Magnet Materials: High-density magnet materials like neodymium iron boron (NdFeB) improve sensitivity and efficiency.
- Magnetic Gap Design: Ensure uniform magnetic gaps to avoid distortion caused by uneven flux distribution.
- Magnetic Circuit Shape: The design of the magnetic circuit affects flux distribution and performance. Optimized shapes reduce distortion.
- Magnetic Circuit Materials: High permeability materials like silicon steel sheets reduce flux leakage.
- Magnetic Circuit Symmetry: Symmetry ensures a uniform magnetic field and reduces distortion.
- Magnetic Circuit Shielding: Shielding reduces external magnetic field interference.
- Magnetic Circuit Cooling: Effective cooling of high-power systems reduces heat buildup.
- Mechanical Stability: Ensure the magnetic circuit remains stable under vibration and shock.
- Integrated Design: Integrating the magnetic circuit with diaphragm and voice coil reduces size and improves compactness.
- Manufacturing Accuracy: High-precision processes improve magnetic circuit consistency.
3. Improve Voice Coil Design
- Choose the Right Material: Copper and aluminum offer good conductivity and strength, essential for efficient voice coil performance.
- Optimize Voice Coil Geometry: The length, diameter, and number of turns affect impedance and sensitivity, and should be optimized for performance.
- Reduce Voice Coil Mass: Thinner or multi-strand wires reduce mass, enhancing response speed and reducing distortion.
- Improve Heat Dissipation: Efficient heat dissipation prevents overheating and maintains performance.
- Mechanical Strength: The voice coil should withstand stress and vibration without deforming or breaking.
- Optimize Support Structure: The voice coil's frame should keep it stable within the magnetic field to avoid additional distortion.
- Advanced Winding Technology: Automated winding machines improve consistency and accuracy in the voice coil design.
- Voice Coil Insulation: Insulation prevents short circuits and improves reliability.
- Heat Treatment: Heat treatment enhances the mechanical properties and stability of the voice coil.
4. Other Improvements for Micro Speaker Drivers
- Diaphragm-Voice Coil Connection: A secure, gap-free connection reduces distortion and improves sound clarity.
- Support Structure of Diaphragm: Use lighter and stronger materials for suspension edges and folding rings to enhance diaphragm movement and reduce distortion.
- Cabinet Design: Optimizing cabinet size, shape, and materials improves low-frequency response in micro speakers.
- Acoustic Damping Materials: These materials reduce cabinet resonance and improve sound clarity.
- Advanced Crossover Technology: High-quality crossovers ensure speaker units work within optimal frequency ranges.
- Digital Signal Processing (DSP): DSP corrects frequency response irregularities, enhancing sound quality.
- Advanced Manufacturing Processes: Precision manufacturing reduces tolerances, ensuring consistent performance.
Comparison Table: Traditional vs Modern Speaker Unit Design
Design Feature | Traditional Speaker Units | Modern Improvements |
---|---|---|
Diaphragm Material | Basic Mylar or Paper | Graphene, PEI, Composite PET |
Magnet Type | Ferrite | Neodymium |
Voice Coil | Standard Copper | CCAW Ultra-fine Windings |
Acoustic Damping | Basic Foam Seal | Engineered Rear Venting |
Sensitivity | ~88dB SPL | 90–103dB SPL |
Frequency Range | 100Hz–10kHz | 60Hz–20kHz |
Use Cases for Improved Speaker Unit Design
Modern advancements in speaker unit design open new doors for various applications, including:
- High-Fidelity Audio Systems: For home theater systems and high-end audio equipment.
- Mobile Devices: Improved sound quality for smartphones, wearables, and portable speakers.
- Automotive Audio: Compact, high-performance speakers for car audio systems.
- Gaming: High-performance speakers for gaming headsets that deliver clear, directional sound.
Conclusion
As the demand for high-quality, compact audio solutions increases, the optimization of speaker unit design becomes critical. By focusing on advancements in diaphragm materials, voice coil technologies, magnetic circuits, and damping systems, OEM manufacturers can create cutting-edge speaker drivers that not only meet but exceed performance expectations across a variety of industries. These improvements in design will ensure that even the smallest speaker drivers can produce clear, dynamic, and rich sound.